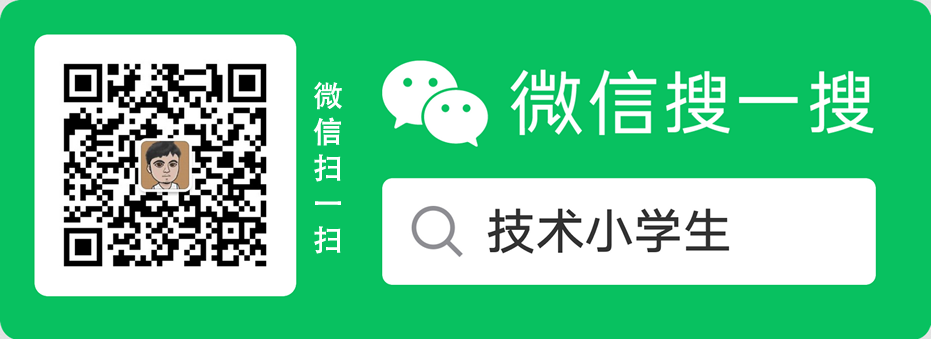
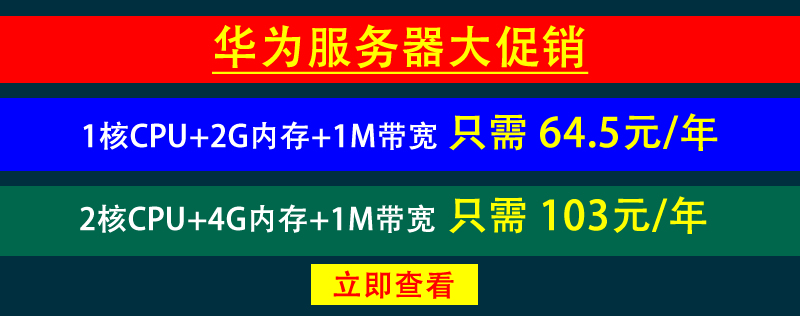
为了对标丰田,这家中国民营汽车企业从2004年引入精益生产,自上而下,全员改善,一点一点地摸索、实践,2016年的改善收益达26亿元,今年的目标则是34亿元。不只是生产追求精益,他们还把精益推进到了非生产环节,就连员工食堂也不例外,员工就餐,一粒米饭都不允许浪费。而看到这样先进的工厂,特斯拉真的也“不过如此”。
信不信由你,这就是今天的长城汽车。
在中国市场,有别于其他汽车企业的大而全,成立于1984年的长城汽车,一直走“专业、专注、专家”路线,业务简单,聚焦战略,稳健发展。其中,皮卡连续19年拿下销量冠军,市占率第一;哈弗SUV连续14年位居销量冠军。
2016年,长城汽车营收直奔千亿,利润过百亿,战略大单品SUV销量超百万辆——这在红海竞争已到“深红”的中国汽车市场,可堪称一枝独秀,甚至盖过合资品牌。
往往中国企业竞相学习丰田模式,却总是不能在企业内部全面落地。但是,长城汽车却做到了,并把精益思想渗透到了企业的血液。从2004年引入精益生产,长城汽车以丰田为标杆,逐步形成了具有特色的长城精益管理模式……
1管理即改善
一句刻在工厂大楼顶部的醒目标语——“每天进步一点点”,是长城汽车的做事理念,也是长城汽车至高无上的企业精神。如同精益生产的核心之一,“持续改善”被长城汽车当做每天去寻求改变的重要准则,哪怕每天改善一点点。
2004年,为了应对汽车市场的竞争,长城汽车董事长魏建军意识到必须通过一种有效的管理模式来提升企业的竞争力。他到日本考察之后,决定引入丰田的精益生产,然后带领长城人全员学习TPS。
为了把精益生产落到实处,长城汽车在每一个环节“疯狂抓执行,玩命提品质”,而不是把精益生产作为一个工具使用。长城汽车副总裁张文辉说,他们践行的精益生产是“全员改善”,称为“自上而下,领导主推;自下而上,培育未来”。
也就是说,高层要变推动为发动;中层要变考核为指导;基层要变被动执行为主动参与,而基层管理者是精益生产实施的主力军。
在精益生产推进过程中,每个员工都要把消除浪费作为立足点,分析和判断生产经营过程中的浪费问题,将其作为目标加以改善。10多年来,全员学习、推进精益生产的事例数不胜数,这些成果被摆在生产车间当样版展示。每一项“成果”节约了多少费用,取得了什么效果都有实实在在的案例。
2对标丰田,细微处见“精益”
据说在丰田的工厂,每一项作业、每一道工序、每一条流程路线都有严格的标准,不容许出现任何的偏差,正所谓追求“零缺陷、零失误”。同时,生产线又要根据客户订单的变化而迅速作出调整。
丰田精益生产的成功,在于解决了生产和销售的衔接问题,也就是所谓的订单式销售。根据顾客的订单进行生产,使生产流程、业务流程以及决策链缩短,减少物流成本和库存成本。这就是精益管理的重要体现。
长城汽车精益管理/成本改善部长吕松说,目前在长城汽车,采用客户订单+销售预测的模式组织生产,大幅度缩短了生产周期及物流周期,满足了顾客的个性化需求。
为了持续的改善,长城人认真研修日本管理文化、工作方法、思维方式,全面学习日企管理。包括高层在内,每一个长城人都要深入现场,通过“用数据说话”挖掘问题真实原因,寻找改进机会,并形成有效的解决办法,为公司降低成本、减少浪费提供新的思路。
公司会经常开展一个叫“创意改善”的活动,鼓励员工参与现场管理,引导员工主动思考,充分发挥他们的智慧,对现场作业浪费提出改善建议。
不只是生产追求精益,长城汽车还把精益推进到了非生产环节。就连员工食堂也不例外。员工就餐,一粒米饭都不允许浪费。并且鼓励食堂也要提升口味。吕松总结说,精益管理就是通过消除所有环节上的不增值活动,达到降低成本、缩短作业周期和改善质量的目的。
而在长城汽车董事长魏建军看来,学习TPS以来,虽然越学越发现自己的差距,但他们坚信已经走上了正确道路,就一定会走到底!
3全员改善的驱动力是什么?
TPS的核心是全员参与,持续改善。
几年前,为了全面推进精益思想,长城汽车还专门成立了精益管理部和精益推进部。前者的职能是总结经验和教训,然后制定下一步推广方案,再负责导入相关培训;后者则进行指导和监督,同时制定与之配套的奖惩制度,用指标拉动全员参与。
全员参与改进机制(以前叫合理化建议实施方案),被纳入到了长城的精益管理体系中。员工通过《创意功夫提案制度》,针对身边的浪费、不合理现象提出自己的改进意见。光是在2006-2016年,长城汽车的创意功夫提案采纳并实施就有196万件,数量惊人。
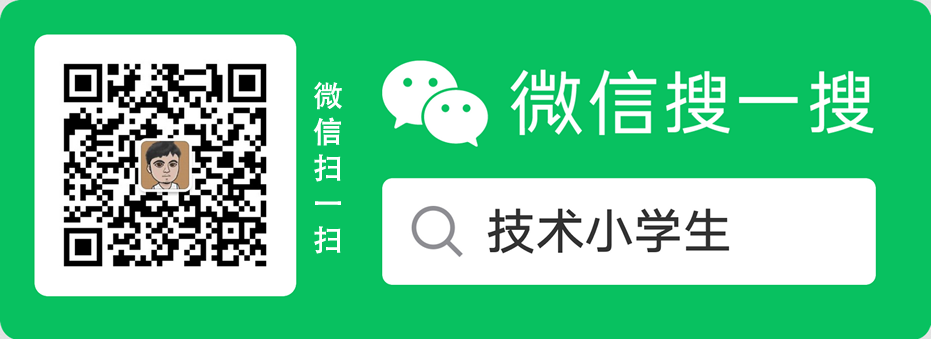
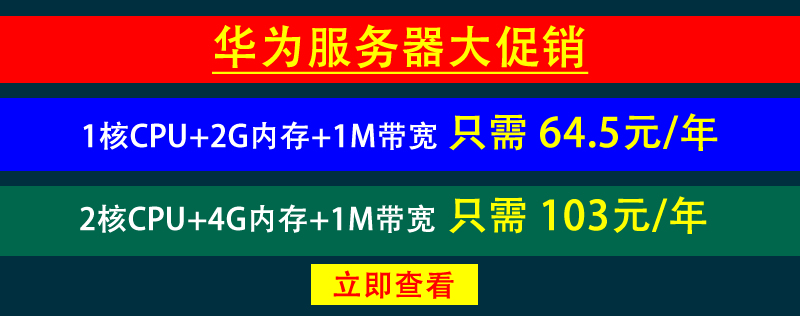
文章评论 本文章有0个评论